Rubber Roller Coverings
- We refurbish existing rubber rollers, cover free issue rollers or manufacture complete new rubber rollers
- In-house engineering support means we can manufacture steel, aluminium or plastic drums and shafts
- We can collect, refurbish and deliver your rubber roller back to you with short lead times
- Over 50 years experience in covering rubber rollers in a range of elastomer materials
Industrial Rubber Roller Coating & Manufacturer Services
With over 50 years of expertise in manufacturing, covering, and refurbishing rubber rollers, Clifton Rubber is your trusted partner for all your rubber roller needs.
We offer a comprehensive range of services tailored to your requirements
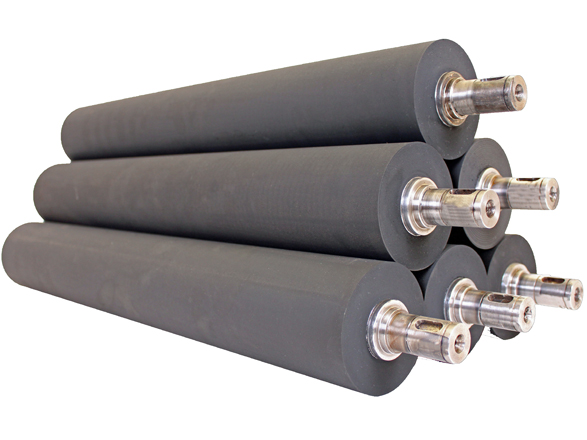
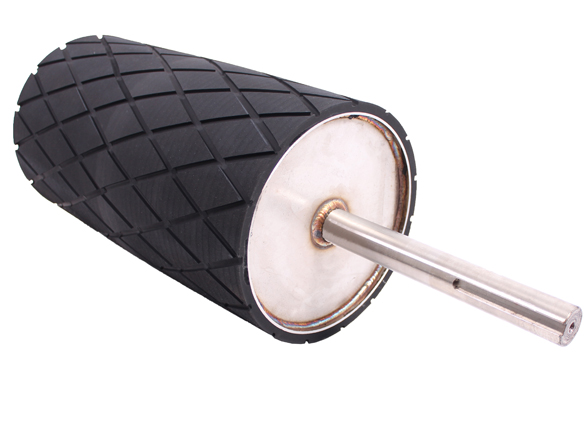
Custom Rubber Roller Coating & Manufacturer Services
At Clifton Rubber, we provide a one-stop shop for all your rubber roller requirements. Our state-of-the-art roller covering and precision engineering equipment, combined with our in-house capabilities, enable us to offer a complete rubber roller manufacturing service. Our capabilities include:
Manufacturing new rubber-covered rollers: We can manufacture complete new rubber rollers, including steel, aluminum, or plastic drums and shafts.
Covering customer-supplied roller drums and shafts: If you have existing roller drums and shafts, we can apply rubber coverings to them, ensuring optimal performance.
Refurbishing worn rubber-covered rollers: We offer refurbishment services for worn rubber rollers. This includes stripping and replacing the existing rubber covering or re-grinding the surface to restore functionality.
We are with you every step of the way
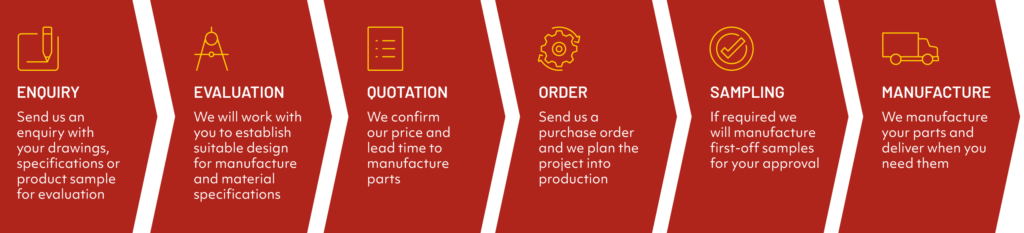
Rubber Roller Covering Service
To make your experience seamless, we provide a hassle-free roller collection and delivery service. We have our own transport network, or we can arrange collection through our trusted logistics partners. Our goal is to offer a fast and reliable roller covering service, accommodating quick turnarounds for breakdown situations.
Our advanced covering, curing and grinding equipment mean we can cover rollers up to 8 meters in length and 3 metres in diameter.
Rollers can be ground to various profiles using our state-of-the-art CNC equipment including: Smooth Parallel Ground, Crowned Ground, Tapered Ground, Polished Finish or alternatively we can supply rollers with Plain Finish,
We can also groove rollers in various patterns including: Helical Groove, Diamond Pattern, Lineal Groove, Spiral Groove, Castellated, Chevron Grooved and Herringbone Groove.


Roller Engineering Service
Our in-house precision engineering division has the latest in CNC machining and fabrication equipment and a team of experienced precision engineers. This in-house engineering capability allow us to keep control of quality and lead times for all our customer’s roller projects.
Our engineering team can manufacture complete new rollers from most engineering materials such as mild steel, stainless steel, aluminium or engineering plastics including nylon and polypropylene. We can also offer an in-house repair service for damaged roller drums, shafts, journals and keyways.
Rubber Roller Materials
We use high quality ethically sourced rubber compounds to cover rollers including but not limited to:
- Natural Rubber (NR)
- Ebonite
- SBR
- Neoprene
- Nitrile
- EPDM
- Hypalon
- Silicone
- Polyurethane
Our polymer compounds can be specified to meet specific performance criteria including food quality, anti-static, conductive and fire retardant.


Roller Applications
The industries we work in are wide ranging including agriculture, pharmaceuticals, food and drink processing, print and packaging, recycling, aerospace and construction to name but a few. Typical roller covering applications include:
- Conveyor Drive and Idler Rollers
- Print Rollers
- Steel Processing Rollers
- Heavy Duty Rollers
- Transfer Rollers
- Materials Handling Rollers
- Agricultural Rollers
- Laminating Rollers
- Squeegee Rollers
- Food Processing Rollers
- Industrial Rollers
- Packaging Rollers
Why Use Clifton Rubber?
Clifton Rubber’s roller covering service is regarded as the best in industry for quality and value. Our rollers are guaranteed, so you can be assured of our commitment to keep your equipment running. Our expert team have accumulated many years’ experience in manufacturing and covering rollers and can advise on any issues or queries including material specifications, roller design or end use applications.
We maintain a certified quality system to ISO9001:2015 to ensure our rubber rollers meet our high-quality standards every time.
Contact us today to discuss your roller covering requirements or book a collection.

-
Aerospace
-
Agriculture
-
Automotive
-
Buildings & Construction
-
Defence
-
Electronic Equipment
-
Food & Drink Processing
-
Manufacturing
-
Marine & Maritime
-
Material Handling
-
Medical Equipment
-
Mining & Quarrying
-
Oil & Gas
-
Paper & Packaging
-
Recycling Equipment
-
Renewables & Power
-
Sport & Leisure
-
Textiles & Clothing
-
Transport
-
Vintage Machinery
-
Water & Sewage
Testimonials
-
“There are a lot of rubber rollers in our food processing plant and Clifton Rubber have always provided a great refurbishment service when our rollers need repairing. We get our rollers back quickly and they are always great quality.”
Brad, Maintenance Engineer, Food Processor
-
“Excellent service which is unusual in this day and age. The polyurethane screening stars do the job great, very very pleased.”
Richard, Owner, Screener Manufacturer
-
“Really pleased we found Clifton rubber, their technical team really helped us in the early stages of our project and now they produce our parts which we know will be top quality every time.”
Sophie, Purchasing Manager
-
“Just to let you know that our new ditch matting that we purchased from you is spot on. Used all through this busy season, really pleased with it.”
Ken, Fairford Bowling Club
-
“Since Clifton Rubber has taken over the re-covering of these gripper pads the customer has had no premature failures and the products have a much longer lifespan.”
Tom, Manufacturing Company
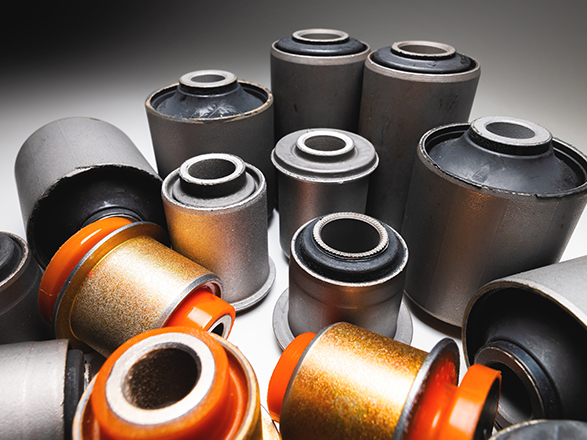
Suspension Bushes for the Transport And Logistics Industry
High-Quality Suspension Bushes for the Transport & Logistics Industry Suspension bushes are critical components in commercial vehicles, reducing vibrations, improving ride stability, and enhancing overall durability. Clifton Rubber manufactures high-quality suspension bushes designed for heavy-duty transport applications, ensuring longevity and reliability in demanding conditions. Custom Suspension Bush Manufacturer & Supplier for the Transport & Logistics…
READ MORE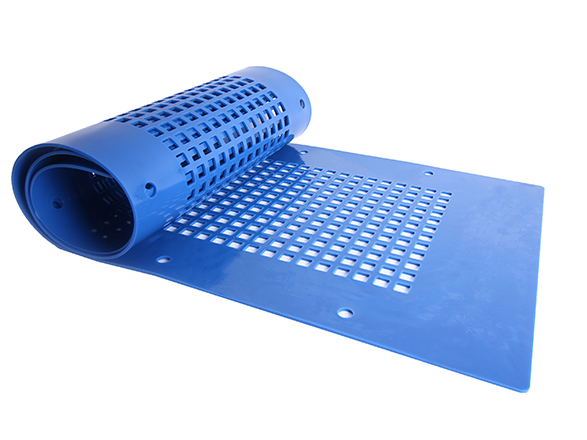
Screening Planks for the Waste And Recycling Industry
High-Performance Screening Planks for the Waste And Recycling Industry In the fast-paced and demanding world of waste and recycling, equipment efficiency and durability are vital. Clifton Rubber manufactures robust screening planks that support effective material separation, increased throughput, and reduced equipment wear. Designed for a range of screening machinery, our rubber screening planks help waste…
READ MORE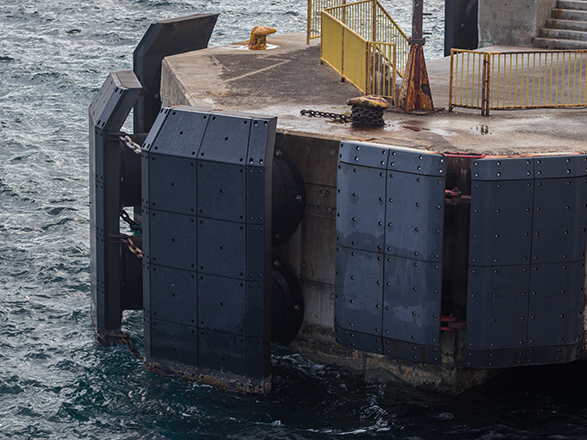
Rubber Fenders for the Transport And Logistics Industry
High-Quality Rubber Fenders for the Transport & Logistics Industry Rubber fenders are essential for safeguarding docks, ports, and vessels by absorbing impact forces during berthing. Clifton Rubber manufactures high-quality rubber fenders designed for durability, impact resistance, and long-term performance, ensuring maximum protection for maritime and logistics operations. Custom Rubber Fender Manufacturer & Supplier for the…
READ MORE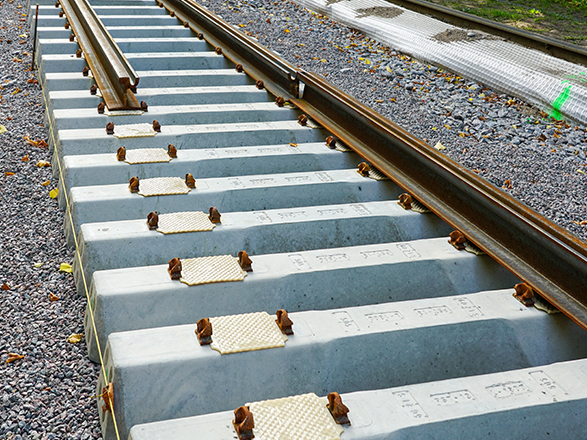
Rail Track Pads for the Transport And Logistics Industry
High-Quality Rail Track Pads for the Transport & Logistics Industry Rail track pads are essential components in railway systems, providing critical cushioning and vibration reduction between the rail and sleeper. Clifton Rubber manufactures high-quality rail track pads designed for durability, noise reduction, and enhanced track longevity, ensuring smooth and efficient railway operations. Custom Rail Track…
READ MORE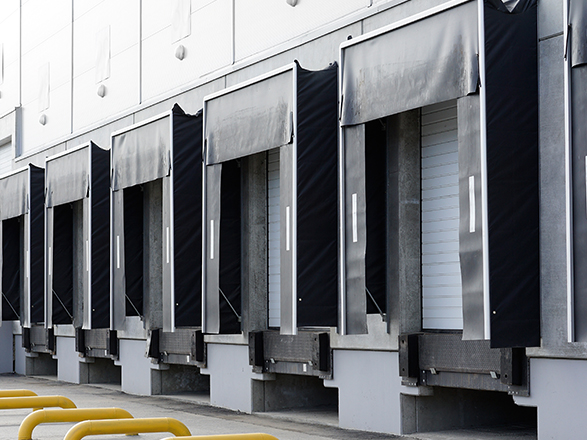
Loading Bay Buffers For The Transport And Logistics Industry
High-Quality Loading Bay Buffers For The Transport & Logistics Industry Loading bay buffers play a crucial role in protecting warehouses, distribution centres, and commercial vehicles from impact damage. Clifton Rubber manufactures high-quality, durable loading bay buffers designed to absorb impact forces, reduce maintenance costs, and improve safety in transport and logistics operations. Custom Loading Bay…
READ MORE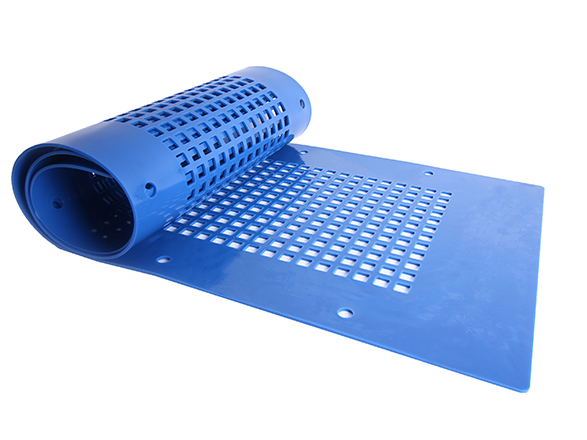
Flip Flow Screen Mats for the Waste And Recycling Industry
Flip Flow Screen Mats for the Recycling Industry In the recycling industry, where materials are often wet, sticky, or irregular in size, traditional screening systems can struggle. Clifton Rubber’s flip flow screen mats offer a powerful solution—flexible, hard-wearing rubber mats that vibrate dynamically to separate even the most challenging materials. Engineered for efficiency and durability,…
READ MORE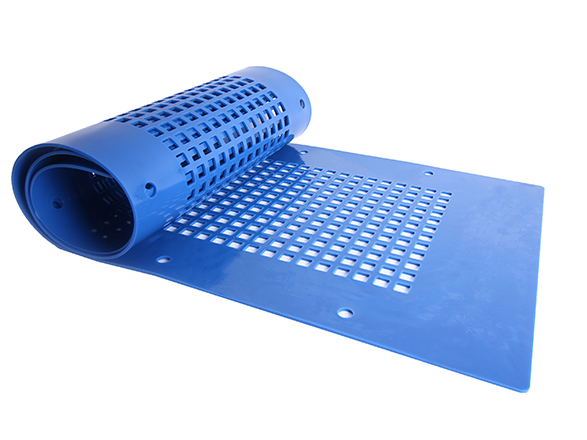
Screening Modules for the Waste And Recycling Industry
Screening Modules for the Waste And Recycling Industry Recycling facilities demand tough, reliable equipment that can perform consistently in challenging environments. At Clifton Rubber, we design and manufacture high-performance rubber screening modules that deliver excellent separation, durability, and ease of maintenance. Whether processing municipal waste, aggregates, plastics, or compost, our screening modules are engineered to…
READ MORE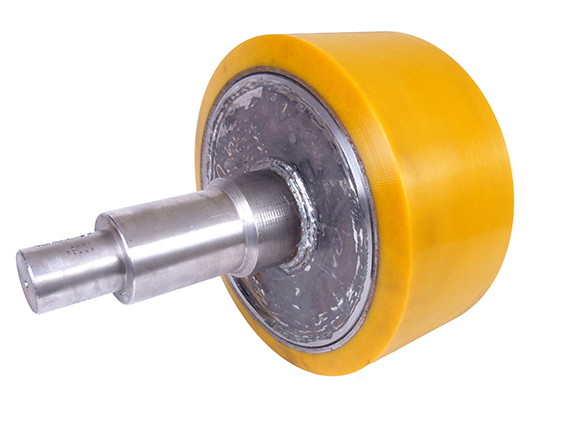
Trommel Wheels for the Waste And Recycling Industry
Trommel Wheels for the Waste And Recycling Industry In the fast-paced and abrasive world of recycling, equipment needs to perform reliably under pressure. Trommel screens—used for sorting and sizing recyclable materials—depend on durable components to keep operations moving efficiently. Clifton Rubber’s trommel wheels are purpose-built to meet these demands, offering a high-performance solution that ensures…
READ MORE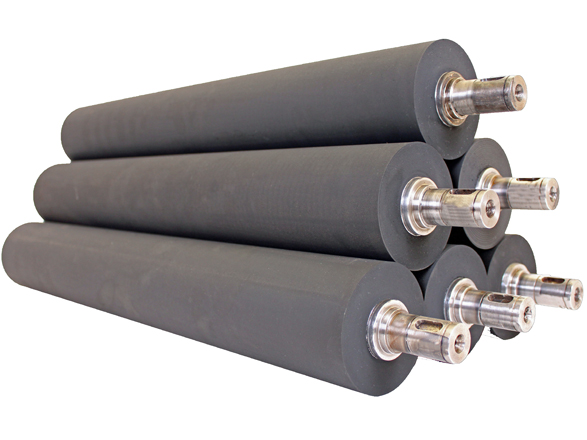
Coating & Laminating Rollers for the Paper & Packaging Industry
Coating & Laminating Rollers for the Paper & Packaging Industry Coating and laminating rollers are indispensable tools in the paper and packaging industry, enabling manufacturers to achieve high-quality finishes and efficient production. Clifton Rubber specialises in crafting durable, high-performance rollers that meet the specific demands of coating and laminating applications. Custom Coating & Laminating Roller…
READ MORE
Ink Transfer Rollers for the Paper & Packaging Industry
Ink Transfer Rollers for the Paper & Packaging Industry Ink transfer rollers play a pivotal role in the printing industry, ensuring accurate and consistent ink distribution for high-quality results. Clifton Rubber specialises in producing durable, high-performance ink transfer rollers that meet the demands of modern printing technologies. Custom Ink Transfer Roller Manufacturer & Supplier for…
READ MORE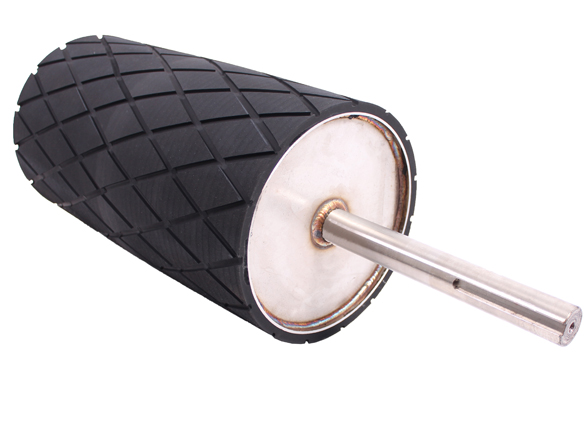
Press Rollers for the Paper & Packaging Industry
Press Rollers for the Paper & Packaging Industry Press rollers are critical components in the paper and packaging industry, facilitating smooth and efficient production processes. Clifton Rubber specialises in manufacturing high-quality press rollers that deliver durability, precision, and superior performance in demanding applications. Custom Press Roller Manufacturer & Supplier for the Paper & Packaging Industry…
READ MORE
Embossing Rollers for the Paper & Packaging Industry
Embossing Rollers for the Paper & Packaging Industry Embossing rollers are indispensable tools in the paper and packaging industry, enabling manufacturers to achieve high-quality finishes and efficient production. Clifton Rubber specialises in crafting durable, high-performance rollers that meet the specific demands of embossing applications. Custom Embossing Roller Manufacturer & Supplier for the Paper & Packaging…
READ MORE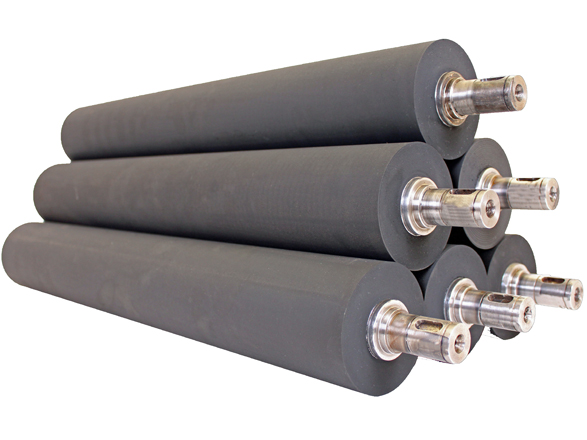
Squeeze Rollers for the Textiles & Clothing Industry
Squeeze Rollers for the Textiles & Clothing Industry Squeeze rollers are essential components in textile processing, helping to remove excess water, chemicals, and other liquids from fabrics during various production stages. Clifton Rubber manufactures premium squeeze rollers designed for durability, precision, and efficiency, ensuring optimal moisture control and fabric treatment. What Are Squeeze Rollers? Squeeze…
READ MORE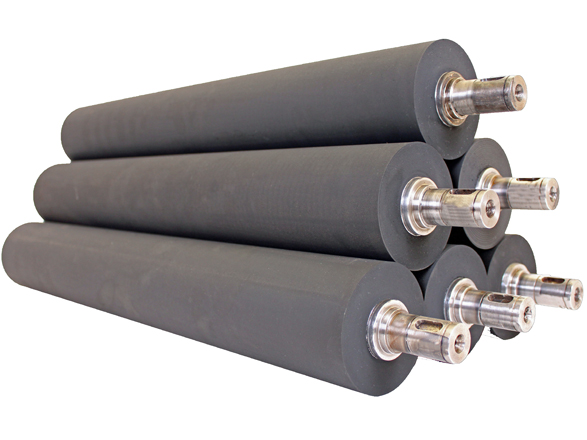
Sizing Rollers for the Textiles & Clothing Industry
Sizing Rollers for the Textiles & Clothing Industry Sizing rollers play a crucial role in textile manufacturing, ensuring fabric strength, smoothness, and uniformity during production. At Clifton Rubber, we specialise in manufacturing precision-engineered sizing rollers that enhance efficiency and product quality in the textiles and clothing industry. Custom Sizing Roller Manufacturer & Supplier for the…
READ MORE
Guide Rollers for the Textiles & Clothing Industry
Guide Rollers for the Textiles & Clothing Industry Guide rollers play a crucial role in textile manufacturing by ensuring proper fabric alignment and smooth movement through production lines. Clifton Rubber manufactures durable and high-performance guide rollers that help optimise efficiency, reduce fabric distortion, and improve overall textile quality. Custom Guide Roller Manufacturer & Supplier for…
READ MORE
Bleaching Rollers for the Textiles & Clothing Industry
Bleaching Rollers for the Textiles & Clothing Industry Bleaching rollers play a critical role in textile manufacturing by ensuring even application of bleaching agents to fabrics, improving whiteness and fabric quality. Clifton Rubber specialises in manufacturing premium bleaching rollers that provide durability, precision, and efficiency for textile processing. Custom Bleaching Roller Manufacturer & Supplier for…
READ MORE
Riser Clamps for the Renewables & Power Industry
Riser Clamps for the Renewables & Power Industry Riser clamps are essential components in the renewables and power industry, ensuring secure and stable support for pipes and cables in demanding environments. Clifton Rubber specialises in designing and manufacturing premium riser clamps tailored for renewable energy and power infrastructure projects. Custom Riser Clamps Manufacturer & Supplier…
READ MORE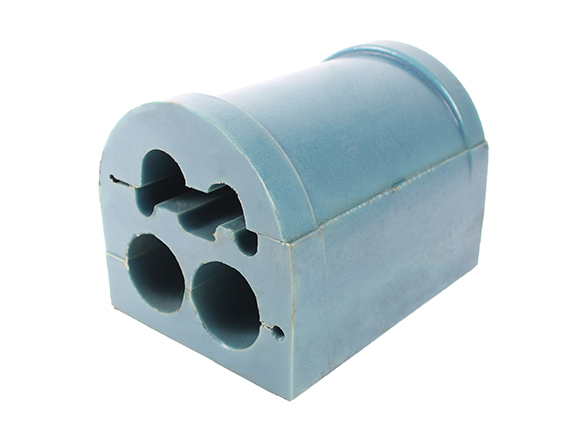
Piggyback Clamps and Saddles for the Renewables & Power Industry
Piggyback Clamps and Saddles for the Renewables & Power Industry Piggyback clamps and saddles play a crucial role in the renewables and power industry, ensuring the secure and efficient installation of cables and pipes. Clifton Rubber provides high-quality solutions designed to meet the rigorous demands of renewable energy projects. Custom Piggyback Clamp and Saddle Manufacturer…
READ MORE
Pipe Laying Rollers for the Renewables & Power Industry
Pipe Laying Rollers for the Renewables & Power Industry Pipe laying rollers are critical tools in the renewables and power industry, ensuring the safe and efficient handling of cables and pipes during installation. Clifton Rubber specialises in manufacturing high-quality vertical, horizontal, and diablo pipe laying rollers, designed to meet the demanding requirements of the sector.…
READ MORE
Cable and Pipe Protectors for the Renewables & Power Industry
Cable and Pipe Protectors for the Renewables & Power Industry Cable and pipe protectors are essential in the renewables and power industry, ensuring the safety and longevity of critical infrastructure. Clifton Rubber specialises in manufacturing high-quality protectors that shield cables and pipes from damage during installation and operation in demanding environments. Custom Cable and Pipe…
READ MORE
Piggyback Clamps and Saddles for the Oil and Gas Industry
Piggyback Clamps and Saddles for the Oil and Gas Industry In the oil and gas industry, ensuring the secure installation of pipelines is critical. Clifton Rubber’s high-performance piggyback clamps and saddles are designed to meet these demands, providing robust solutions for pipeline attachment and stabilisation. Our clamps and saddles are manufactured to the highest standards,…
READ MORE
Cable and Pipe Protectors for the Oil and Gas Industry
Cable and Pipe Protectors for the Oil and Gas Industry In the demanding environments of the oil and gas industry, protecting cables and pipes is critical to ensure operational efficiency and safety. Clifton Rubber’s high-quality cable and pipe protectors are designed to shield essential infrastructure from impact, abrasion, and environmental damage. Our protectors are trusted…
READ MORE
Cable Sheath Linings for the Oil and Gas Industry
Cable Sheath Linings for the Oil and Gas Industry Cables are critical components in the oil and gas industry, carrying power, signals, and data across vast and often challenging environments. Clifton Rubber’s cable sheath linings provide an essential layer of protection, ensuring optimal cable performance and longevity. Our linings are designed to withstand extreme conditions,…
READ MORE
Pipe Laying Rollers for the Oil and Gas Industry
Pipe-Laying Rollers for the Oil and Gas Industry In the oil and gas industry, where precision and reliability are paramount, pipe-laying rollers play a critical role. Clifton Rubber offers high-quality vertical, horizontal, and diablo pipe-laying rollers, designed to facilitate efficient and safe pipe installation in offshore and onshore projects. Our rollers are engineered to withstand…
READ MORE
Rubber Buckle Covers for the Defence Industry
Rubber Buckle Covers for the Defence Industry In the demanding environments of the defence industry, protecting essential fastening systems is crucial. Rubber buckle covers from Clifton Rubber provide robust protection for straps, harnesses, and fastening systems, ensuring their functionality and durability during critical operations. Engineered with precision, our rubber buckle covers are built to withstand…
READ MORE
Aerial Protectors for the Defence Industry
Aerial Protectors for the Defence Industry In the defence industry, where reliability and precision are critical, protecting sensitive equipment like communication aerials is a top priority. Clifton Rubber offers high-quality aerial protectors designed to shield military vehicle antennas from damage during operation. These protectors ensure consistent communication, reduced maintenance costs, and enhanced operational efficiency in…
READ MORE
Tank Wheels for the Defence Industry
Tank Wheels for the Defence Industry Tank wheels are critical to the operational success of military vehicles, providing the strength, durability, and reliability needed for extreme conditions. At Clifton Rubber, we specialise in designing and manufacturing tank wheels that meet the rigorous demands of defence applications. Our wheels ensure consistent performance, extended lifespan, and superior…
READ MORE
Anti-Vibration Mounts for the Defence Industry
Anti-Vibration Mounts for the Defence Industry In the defence industry, where precision and reliability are paramount, controlling vibrations is critical to maintaining the integrity and performance of equipment. Clifton Rubber manufactures high-quality anti-vibration mounts tailored to meet the demanding requirements of military and ddefenceapplications. These mounts ensure stability, extend equipment life, and optimise operational efficiency…
READ MORE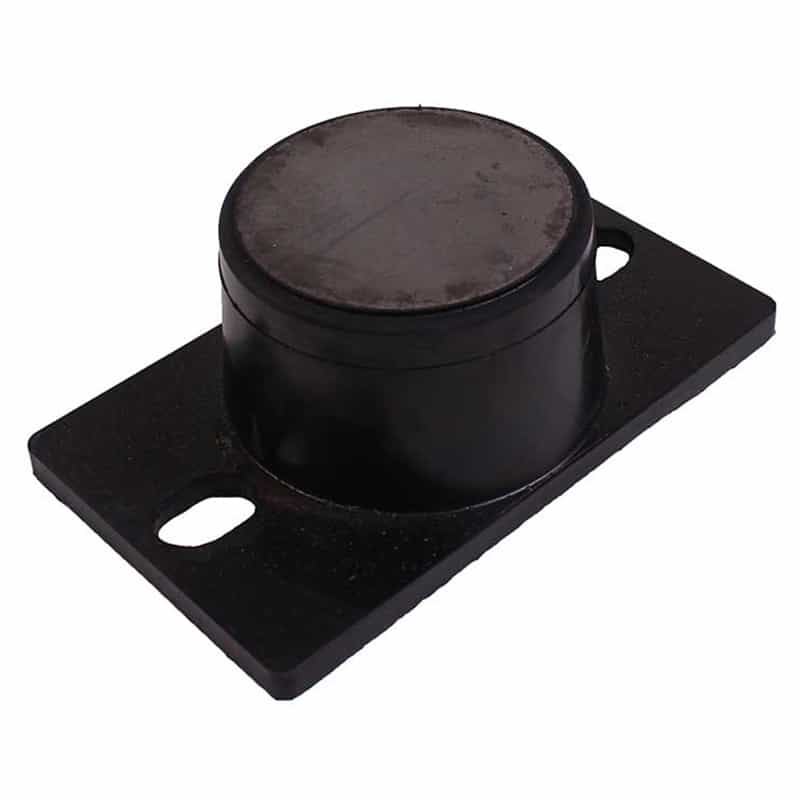
Heavy-Duty Bucket Bump Stops for Construction Equipment
Heavy-Duty Bucket Bump Stops for Construction Equipment Bucket bump stops are essential components in heavy machinery used in the construction industry. At Clifton Rubber, we specialise in manufacturing robust rubber bump stops designed to protect both machinery and materials during operation. Our bump stops are engineered to withstand the harsh conditions of construction environments, providing…
READ MORE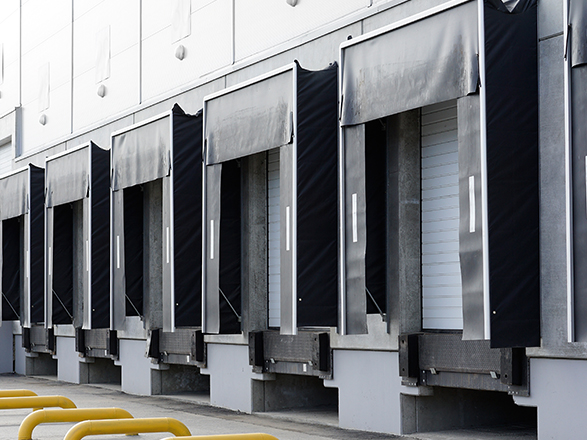
Durable Dock Buffers for the Construction Industry
Durable Dock Buffers for the Construction Industry Dock buffers are essential for protecting loading bays and vehicles during the loading and unloading process, ensuring both safety and efficiency. At Clifton Rubber, we manufacture high-quality rubber dock buffers designed to withstand heavy impact and provide long-lasting protection. Our products are engineered to handle the rigorous demands…
READ MORE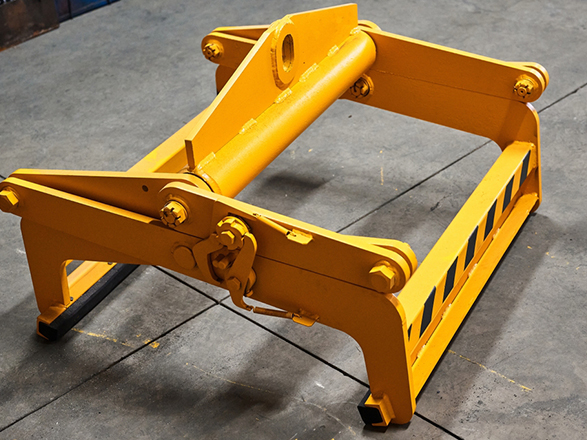
Efficient Brick Grabs for the Construction Industry
Efficient Brick Grabs for the Construction Industry Brick grabs are specialised lifting devices designed to securely grip and transport bricks. They are typically used with cranes or forklifts and can accommodate various sizes and weights of bricks. Clifton Rubber offers a range of brick grabs tailored to meet the diverse needs of the construction industry,…
READ MORE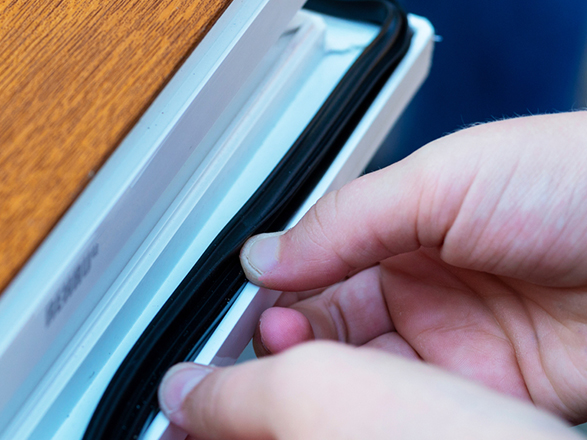
Durable Rubber Window Seals for the Construction Industry
Durable Rubber Window Seals for the Construction Industry Rubber window seals play a vital role in ensuring that buildings are energy-efficient, well-insulated, and protected from external elements. At Clifton Rubber, we specialise in producing top-tier rubber window seals that cater to the diverse needs of the construction industry. Our seals are engineered for durability, performance,…
READ MORE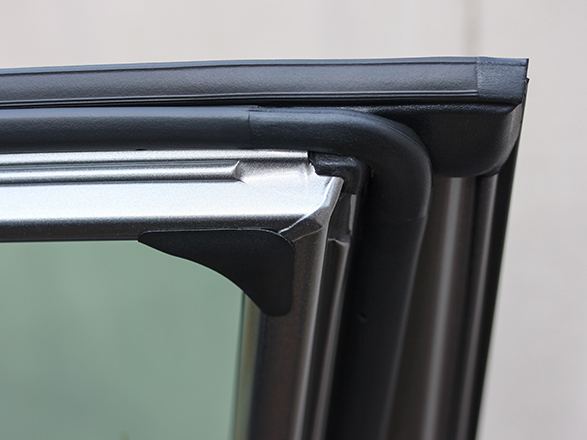
Durable Door Seals for the Automotive Industry
Durable Door Seals for the Automotive Industry Door seals are vital components in vehicles, providing a secure fit between the door and the vehicle’s frame. They are designed to prevent water, air, and noise from entering the cabin, enhancing comfort and driving experience. At Clifton Rubber, we manufacture high-quality door seals that meet the rigorous…
READ MORE
Engine Mount Products for the Automotive Industry
Engine Mount Products for the Automotive Industry Engine mounts are essential components in any vehicle, playing a crucial role in reducing engine vibration and ensuring engine stability. At Clifton Rubber, we specialise in producing high-quality engine mounts that meet the demands of modern vehicles, delivering improved performance, comfort, and durability. Custom Engine Mounts Manufacturer &…
READ MORE
Buffer Products for the Automotive Industry
Buffer Products for the Automotive Industry Buffers play a critical role in the automotive industry by absorbing shocks, reducing vibration, and protecting vital components from damage. At Clifton Rubber, we specialise in designing and manufacturing top-tier buffers that enhance vehicle performance and durability, ensuring safety and longevity for both vehicles and their components. Custom Buffer…
READ MORE
Rubber Hose Products for the Automotive Industry
Rubber Hose Products for the Automotive Industry Rubber hoses play a critical role in the automotive sector, ensuring the efficient transport of fluids like fuel, coolant, and brake fluid throughout vehicles. At Clifton Rubber, we specialise in producing durable, reliable, and versatile rubber hoses designed to meet the exacting standards of the automotive industry. Bespoke…
READ MORE
Track Wheels Recovered for Agricultural Customer
We were recently approached by a customer in the Agricultural Industry to re-cover his existing John Deere Track Wheels.
READ MORE
A Rubber Diaphragm for a Leading Pump Manufacturer
We were approached by a leading pump OEM to manufacture an advanced rubber diaphragm for their new range of diaphragm pumps.
READ MORE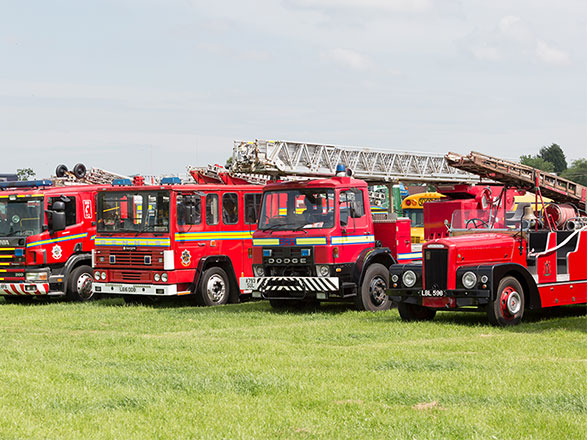
Wheel Covering Project for Vintage Fire Engine
At Clifton Rubber we cover all types of wheels, some of which can be found on vintage machinery.
READ MORE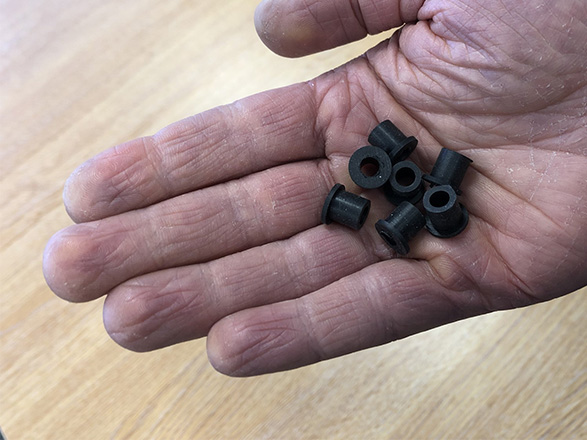
Quality Wins a New Rubber Moulding Customer
We were recently approached by a long-established UK manufacturing company to produce a rubber collet which was bespoke to their needs.
READ MORE
Bespoke Polyurethane Manufacturing Project
We were recently approached by a company enquiring if we could manufacture a very specialised, bespoke polyurethane product for them.
READ MORE
Enlightening Polyurethane Moulding Solution
We have recently completed a new polyurethane moulding project for a leading British manufacturer of external lighting.
READ MORE
Polyurethane Solution for Lifting Equipment
We have just completed a successful polyurethane moulding project for a Maintenance company specialising in Lifting Equipment.
READ MORE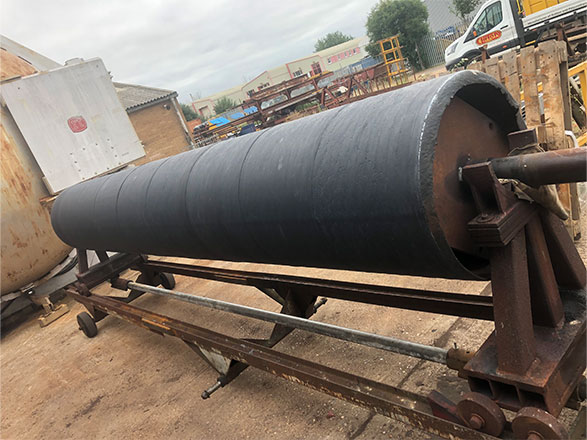
Rubber Roller Project Provides Subsea Solution
Always striving to offer bespoke solutions to meet specific customer requirements, in whatever industry, we recently worked on a rubber roller covering project for a company in the Offshore industry.
READ MORE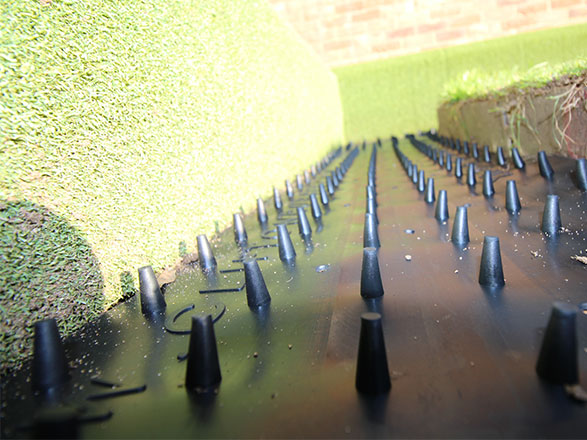
Bowls Club Reflects on Ditch Liners’ Quality
Bowling Club Reflects on Ditch Liners’ Quality and Longevity after 3 Years of Use
READ MORE
PU Moulding Project for Hospitality Sector
We have recently successfully completed an interesting project for a new consumer products company. The customer required a bespoke polyurethane drip tray moulding, which would form part of a new piece of high-end bar equipment.
READ MORE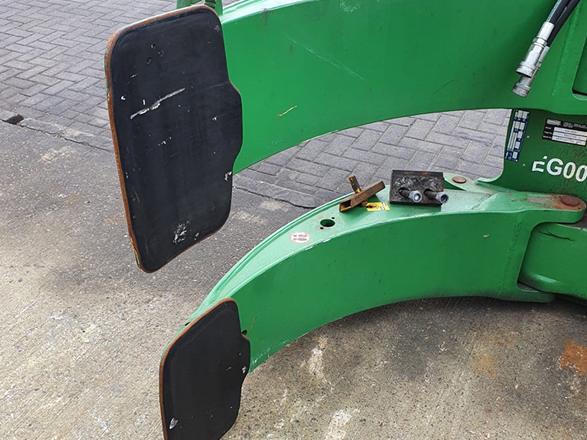
Customer Saves with New Rubber Covered Gripper Pad
Unhappy with the quality of rubber gripper pads used on their machines, a new customer approached us to find a solution to limit the downtime they were experiencing on their machines.
READ MORE
Water Valve Linining Project
rubber moulding project pic Bespoke Rubber Air Valve Lining Project Successfully Delivered to an Engineering Solutions Customer
READ MORE