Industrial Electronic Rubber Component Manufacturer & Supplier
We provide solutions to meet our customer’s specific rubber and polyurethane product requirements in the electronic equipment industry. The components we manufacture are used by our customers in various applications across the industry.
Rubber components are commonly used in electronic equipment for various purposes due to its hard wearing properties, such as insulation, sealing, vibration damping, and protection.
Custom-moulded rubber components have been designed for specific customer applications, such as rubber seals, rubber cable protectors, rubber diaphragms and anti vibration mounts and rubber connectors.
From moulding processes to precision engineering, discover how these components play an essential role in enhancing the electronic equipment industry.

To find out more about each of our Capabilities in the Electronics Industry…
Read MoreCustom Water & Sewage Treatment Rubber Parts Manufacturing Services
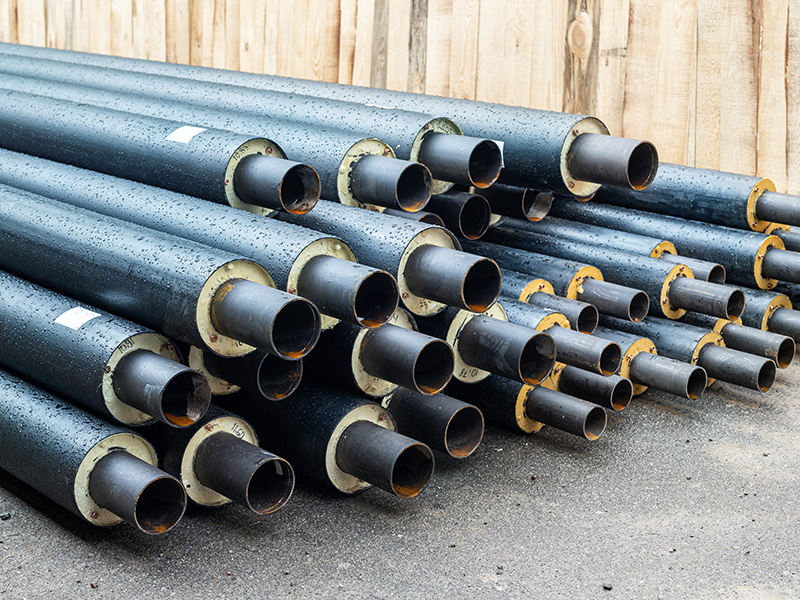
Rubber Moulding For The Electronic Equipment Industry
Rubber moulding offers numerous benefits to the electronic equipment industry. It allows the production of complex and precise rubber components, catering to the technicalities of this market. Rubber moulding techniques allow high levels of precision, ensuring uniform product quality. This method offers adaptability, as rubber moulds can be customised to match specific shapes, sizes, and tolerances.
This adaptability leads to cost-efficiency and streamlined production processes, minimising material waste. Moreover, rubber moulding enhances product longevity by providing exceptional resistance to chemicals, abrasion, and impact. With its capacity to fabricate detailed designs and endure harsh conditions, rubber moulding stands as an optimal choice for applications within the electronic equipment industry.
Here are some common uses of rubber moulded components in in the electronic equipment industry:
- Gaskets: to create watertight and airtight seals in electronic enclosures, preventing moisture, dust, and other contaminants from entering sensitive electronic components.
- Seals and O-rings: to prevent the leakage of liquids or gases in electronic equipment.
- Keypads and Buttons: used in electronic devices such as remote controls, keyboards, and control panels, providing tactile feedback and reliable operation.
- Shock Absorbers and Vibration Dampers: Rubber components are used to absorb shocks and dampen vibrations in electronic equipment, protecting delicate components from damage due to mechanical stress.
- Insulating and Conformal Coatings: Rubber materials are used as insulating coatings or conformal coatings to protect electronic circuitry from moisture, dust, and electrical interference.
- Anti-slip Pads and Feet: Rubber pads and feet are used to provide stability and prevent slippage for electronic devices such as computers, monitors, and audio equipment.
Polyurethane Moulding For The Electronic Equipment Industry
Polyurethane moulding provides exceptional versatility, allowing for the production of a wide range of products with varying shapes, sizes, and hardness levels. Utilising polyurethane moulding enables the creation of complex and intricate designs, ensuring precise and consistent product quality. This process also offers excellent resistance to abrasion, impact, and chemicals, resulting in durable and long-lasting products. It also provides insulation properties, making it suitable for applications requiring thermal or electrical insulation.
Additionally, polyurethane moulding allows for efficient mass production, reducing production time and costs.
Some polyurethane components used in the electronic industry include:
- Polyurethane Dampers and Vibration Isolators: to help reduce vibration and noise in electronic equipment, improving its performance and longevity.
- Polyurethane Seals and Gaskets: to create airtight or watertight seals in equipment.
- Polyurethane Dampers and Vibration Isolators: to help reduce vibration and noise in electronic equipment, improving its performance and longevity.
- Polyurethane Seals and Gaskets: to create airtight or watertight seals in equipment.
- Polyurethane Dampers and Vibration Isolators: to reduce vibration and noise in machinery and equipment.
- Insulating Bushings and Spacers: Polyurethane bushings and spacers are used for insulating and spacing electronic components within assemblies. They provide electrical insulation and mechanical support while withstanding environmental factors such as heat, chemicals, and vibrations.
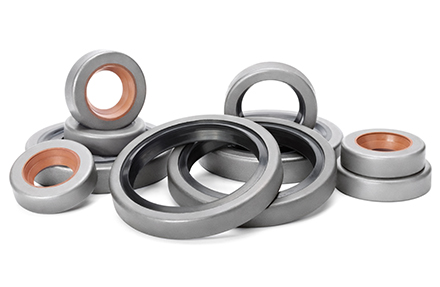

Rubber Covering including
- Rubber Rollers For The Electronic Equipment Industry
- Rubber Wheels & Tyres For The Equipment Industry Industry
Rubber covering plays a pivotal role in the electronic equipment industry, and helps to ensure the reliability and longevity of electronic devices and systems. Here are several ways rubber covering is utilised specifically in this industry.
With its versatility and protective properties, rubber covering offers significant benefits to manufacturers of electronic equipment.
Rubber covering is an indispensable element in the electronic equipment industry, contributing significantly to the protection, functionality, and reliability of electronic devices and systems in diverse operational scenarios.
Rubber Rollers For The Electronic Equipment Industry
Rubber rollers offer a multitude of benefits, including material handling, steadfast product quality, and enhanced production efficiency. With exceptional traction capabilities, rubber rollers guarantee precise alignment and seamless material movement throughout processing stages.
Our range of rubber rollers can be custom made to precise industry demands, spanning hardness variations, surface finishes, and dimensional specifications. This bespoke adaptability ensures optimal performance across a spectrum of electronic applications, aligning seamlessly with the industry’s evolving needs and standards.
Rollers are used in various applications in the electronic equipment industry including:
- Printed Circuit Board (PCB) Handling: Rubber rollers are employed in PCB manufacturing and assembly lines to guide, support, and transport PCBs through various stages of production, ensuring smooth and precise movement without causing damage to delicate components.
- Surface Mount Technology (SMT) Placement: Rubber rollers aid in the accurate placement of surface mount components onto PCBs during SMT assembly. They help to align components with solder paste deposits, ensuring proper positioning before soldering.
- Conveyor Systems: Rubber rollers are integrated into conveyor systems to facilitate the efficient transportation of electronic components, PCBs, and finished products between different production stages. They provide traction and stability, ensuring steady movement along the assembly line.
- Testing and Inspection Equipment: Rubber rollers assist in the smooth movement of electronic devices or components through testing and inspection equipment, allowing for thorough examination and quality control measures to be conducted.
Rubber rollers contribute to the efficiency, precision, and reliability of manufacturing processes within the electronic equipment industry, playing integral roles in handling, assembly, packaging, and quality control operations.


Rubber Wheels & Tyres For The Electronic Equipment Industry
Rubber wheels and tyres have specialised applications in the electronic equipment industry, particularly in the realm of material handling and mobility solutions. Here’s how they are commonly used:
Rubber wheels are used for applications such as:
- Material Handling Equipment: on carts, trolleys and trucks.
- Conveyor Systems: to transport goods in manufacturing plants
- Forklifts, lorries and vans: used in factories and for distribution of goods
- Trolleys and Carts: to transport goods
- Testing and Inspection Equipment: Rubber wheels are used in testing and inspection equipment that moves electronic devices or components through various stages of quality control processes.
Like all our products, rubber wheels and tyres can be designed and customised to match specific load capacities, dimensions, and performance requirements. With their reliability and versatility, rubber wheels and tyres help manufacturers optimise their production efficiency.
Rubber Extrusion For The Electronic Equipment Industry
Rubber extrusion is a valuable process for the manufacturing industry, offering several benefits. It allows for the production of continuous lengths of rubber profiles, seals, gaskets, and other custom shapes with consistent cross-sectional dimensions. Rubber extrusion provides versatility in design, enabling manufacturers to create complex profiles and meet specific requirements for various applications.
This process ensures high precision and dimensional accuracy, resulting in reliable and efficient products. Rubber extrusion offers excellent resistance to environmental factors, chemicals, and temperature fluctuations, enhancing product durability and performance. It also facilitates cost-effective mass production, reducing material wastage and improving overall production efficiency.
Rubber extrusions are used in electronic equipment industry in the following ways:
- Seals and Gaskets: to prevent the leakage of liquids, gases, or dust between two surfaces.
- Bumpers and Protection: to prevent damage from collisions, absorb shock, and protect both the equipment and personnel.
- Conveyor Belts: for material handling.
- Tubing and Hoses: in various industries.
- Cable Management: Rubber extrusions are used for cable management purposes, including cable guides, channels, and grommets. They provide protection for cables and wires, preventing abrasion, tangling, and damage from sharp edges or protrusions within electronic devices and enclosures.
- Soundproofing and Vibration Damping: to reduce noise and vibration levels.
Cable Management: Rubber extrusions are used for cable management purposes, including cable guides, channels, and grommets. They provide protection for cables and wires, preventing abrasion, tangling, and damage from sharp edges or protrusions within electronic devices and enclosures.


Rubber Sheets Conversion For The Electronic Equipment Industry
Rubber sheet conversion allows for the customization and fabrication of rubber sheets to meet specific requirements for various applications. The process enables the production of sheets with precise thickness, dimensions, and properties, providing versatility in product design and functionality.
Rubber sheeting is used for various applications in the electronic equipment including:
- Vibration Isolation
- Electrical Insulation
- Soundproofing
- Shock Absorption
- Thermal Insulation
- Gaskets and Seals and Linings
- Protective Pads and Bumpers and Cushioning
In summary, rubber sheeting serves multiple functions in the electronic equipment industry, including insulation, vibration damping, shock absorption, sealing, thermal management, safety enhancement, and electromagnetic shielding, contributing to the reliability, performance, and longevity of electronic devices and systems.
Precision Engineering For The Electronic Equipment Industry
Precision engineering is highly important in the electronics industry, offering substantial benefits. It encompasses the fabrication of ultra-precise components and devices utilising state-of-the-art methodologies and technologies. Precision engineering guarantees unparalleled accuracy, facilitating the development of intricate electronic parts with precise tolerances.
Our precision engineering expertise provides unparalleled customization and adaptability, catering to the unique demands of the electronics sector.
Clifton Rubber offers a range of Bespoke Rubber Components for various industry sectors, including Electronics. Our custom made products for your industry include:
We also provide Custom Polyurethane solutions tailored to specific industry needs.
